The process of manufacturing stainless steel pipes involves several stages, from raw material selection to the final product. Here's a simplified breakdown of the process:
1. Raw Material Selection
- Stainless Steel Alloys: The raw material for stainless steel pipes is typically an alloy of iron, chromium (at least 10.5%), and other elements like nickel, molybdenum, and manganese. The alloy's composition is chosen depending on the intended application of the pipe (e.g., 304, 316, 201, etc.).
2. Melting & Casting
- Melting: The raw materials (metal scrap, ferrochrome, nickel, etc.) are melted in an electric arc furnace (EAF). This produces the base stainless steel.
- Casting: The molten stainless steel is then cast into solid shapes called billets or slabs. These billets serve as the foundation for producing the pipe.
3. Forming (Hot or Cold)
There are two common methods for shaping stainless steel pipes: stainless seamless steel pipe and stainless steel welded pipe.
4. Heat Treatment (Annealing)
- After the pipes are formed, they undergo an annealing process. The pipes are heated to a high temperature and then rapidly cooled (quenched) to relieve stresses, improve ductility, and restore the desired material properties (such as corrosion resistance).
5. Pickling and Passivation
- Pickling: Stainless steel pipes are immersed in an acidic solution (usually a mixture of nitric acid and hydrofluoric acid) to remove scale, oxide layers, and impurities that may have formed during the heat treatment process.
- Passivation: After pickling, the pipes undergo passivation, which involves exposing them to an oxidizing solution to form a protective chromium oxide layer. This layer increases the pipe's resistance to corrosion.
6. Sizing and Straightening
- The pipes are then sized to their final dimensions, both in terms of outer diameter and wall thickness.
- A straightening machine is used to ensure that the pipe is perfectly straight along its entire length, as any bends or deviations would affect its functionality.
7. Surface Treatment
- Depending on the intended use, the pipes may undergo additional surface treatments to improve their appearance or enhance their corrosion resistance.
- Polishing: The pipes may be polished to create a smooth, shiny surface (common for architectural and decorative uses).
- Grinding or Brushing: Pipes may also be ground or brushed for a matte or satin finish.
8. Testing and Quality Control
- Dimensional Inspection: The pipes are checked for compliance with specifications in terms of length, diameter, and wall thickness.
- Non-Destructive Testing (NDT): Methods such as ultrasonic testing (UT), eddy current testing, or X-ray inspections are used to ensure the integrity of the pipe.
- Hydrostatic Testing: Pipes are subjected to high pressure to ensure they can withstand operating conditions without leaking or bursting.
9. Cutting and Packaging
- The pipes are cut to the required lengths or spooled for further processing.
- They are then packaged and labeled according to customer requirements for shipping or further assembly.
10. Delivery
- Finally, the stainless steel pipes are ready for delivery to customers or further processing, such as bending, welding, or fitting into a larger system.
This process ensures that stainless steel pipes meet industry standards for strength, durability, and corrosion resistance, making them suitable for a wide range of applications including construction, plumbing, oil & gas, food processing, and more.
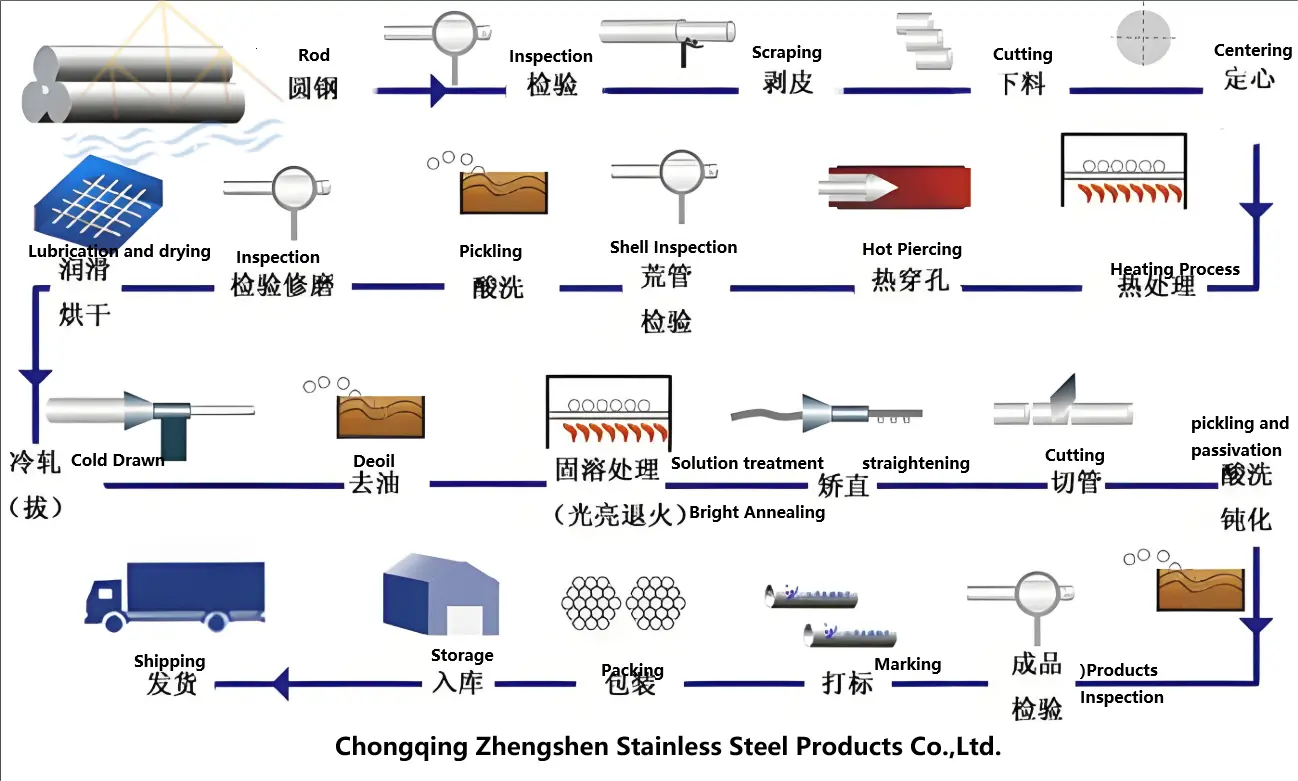